網站首頁
Website Home
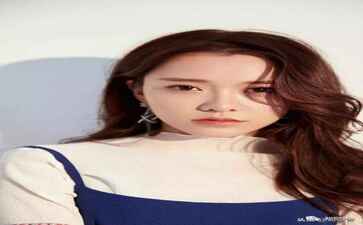
岳池縣組礎舞臺燈光音響設備有限公司位于岳池縣,岳池縣組礎舞臺燈光音響設備有限公司www.jingpinhang.cn經營范圍含:圖書、化工設備、電信設備、塑料工藝品、無機顏料、廢金屬處理設施、乳制品、越野汽車、摩托車配件、攪拌機(依法須經批準的項目,經相關部門批準后方可開展經營活動)。。
岳池縣組礎舞臺燈光音響設備有限公司遵照黨中央、國務院關于國有企業深化改革的戰略部署,我們將緊密圍繞國資委提出的做大、做強企業的核心要求,堅定不移地推動企業改革進程。我們將進一步優化產業結構,合理配置資源,以提升企業的核心競爭力為關鍵,全面提升企業的整體素質和經營能力。同時,我們將積極面向國際、國內兩個市場,努力開拓新的發展空間,向著更加遠大、宏偉的目標不斷奮斗,為實現企業的可持續發展和國家的繁榮富強貢獻力量。
岳池縣組礎舞臺燈光音響設備有限公司在發展中注重與業界人士合作交流,強強聯手,共同發展壯大。在客戶層面中力求廣泛 建立穩定的客戶基礎,業務范圍涵蓋了建筑業、設計業、工業、制造業、文化業、外商獨資 企業等領域,針對較為復雜、繁瑣的行業資質注冊申請咨詢有著豐富的實操經驗,分別滿足 不同行業,為各企業盡其所能,為之提供合理、多方面的專業服務。
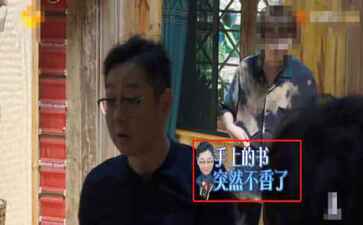
岳池縣組礎舞臺燈光音響設備有限公司秉承“質量為本,服務社會”的原則,立足于高新技術,科學管理,擁有現代化的生產、檢測及試驗設備,已建立起完善的產品結構體系,產品品種,結構體系完善,性能質量穩定。
岳池縣組礎舞臺燈光音響設備有限公司是一家具有完整生態鏈的企業,它為客戶提供綜合的、專業現代化裝修解決方案。為消費者提供較優質的產品、較貼切的服務、較具競爭力的營銷模式。
核心價值:尊重、誠信、推崇、感恩、合作
經營理念:客戶、誠信、專業、團隊、成功
服務理念:真誠、專業、精準、周全、可靠
企業愿景:成為較受信任的創新性企業服務開放平臺
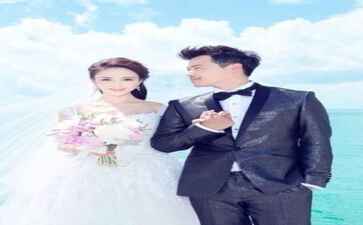